This article was written by Dynautics founder and CEO, Dr Henry Robinson, and subsequently published in The Digital Ship, Maritime Journal and the September/October 2021 edition of RINA’s Ship & Boat International.
Henry has a degree in Physics and a PhD in Electronic Engineering and has been working in marine electronics and autopilots for the last 25 years.
The design and build of uncrewed surface vessels (USVs) is complex and challenging. Hundreds of decisions relating to mission goals, payload requirements, power budget, hull design, communication systems and propulsion control and management need to be analysed and implemented.
Crewed vessel builders often rely on single-source suppliers for propulsion and instrumentation to help the crew control the vessel. In the case of an uncrewed (or partially crewed) vessel, the builder needs to replace elements of the human interface with a remote human interface. Creating remote-control capability for propulsion systems requires interaction with their internal communications, which are often proprietary and closed. Companies such as Torqeedo, Volvo, Mercury and many others provide control interfaces that are designed for manned operation. For uncrewed vessels, enhanced control interfaces are required to make the designer’s task easier.
- SEA-KIT USV
- HRW ARC boat
- HydroSurv REAV USV
Technical considerations
Uncrewed surface vessels vary in size from under 1 metre LOA to 20 metres and beyond, with displacements ranging from a few kilograms to many tonnes. Unsurprisingly therefore, propulsion systems cover a wide range of power levels, interfaces and technologies.
Interface types (broadly) in order of size/power:
- PWM-controlled Electronic Speed Controllers for simple electric motors
- Serial bus, using ASCII-coded commands
- Serial bus using binary protocols
- Analogue interfaces found on many larger vessels
- Proprietary CANbus protocols used by various engine manufacturers
- Proprietary CANbus protocols used by manufacturers of generic engine controls
While many of these protocols carry demands to the propulsion, most of them do not bring back any status information. Feedback of achieved RPM may come from tacho pulses or from built-in sensors that generate CAN or serial data. Other sensors may be fitted, such as current sensing on electric motors, which can give an indication of power delivered.
Safety is of course a critical concern, especially at high power levels, but even a small propeller can cause damage or injury and the control system needs to be designed with this in mind. This is particularly important in handover protocols for optionally manned boats.
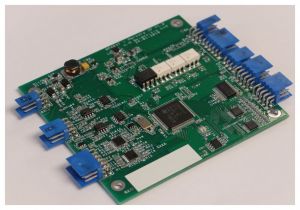
MIM Mercury Interface Module
A frequent challenge faced in the control of USVs is the achievement of a smooth response from full astern to full ahead. Crewed vessels usually have a detent behaviour, with a wide deadband around the stop position. To achieve accurate control of differential steering, the control system needs to compensate for this deadband. Internal combustion engines tend to drive through a gearbox, with an inevitable sudden change when the gearbox engages which the control system must take into account. Waterjets are the exception to this, as they adjust smoothly through the zero point. Electric drives often have a similar deadband built in, so again the control system needs to be designed to preserve this behaviour for a man on board, but smooth it out for automatic control, for example for low-speed manoeuvring and Dynamic Positioning.
Dynautics has developed a wide range of solutions to drive propulsion and steering from a few Watts up of 1,000 hp or more, from electric to internal combustion and even for sail vessels and wave propulsion. Our years of experience tell us that there will be yet more variety in the years to come in the exciting, fast-moving marine autonomy sector.